What is Porosity in Welding: Common Resources and Efficient Solutions
Wiki Article
Porosity in Welding: Identifying Common Issues and Implementing Best Practices for Avoidance
Porosity in welding is a prevalent problem that usually goes undetected until it creates substantial problems with the stability of welds. In this conversation, we will certainly check out the vital aspects adding to porosity formation, examine its destructive results on weld performance, and discuss the best techniques that can be embraced to decrease porosity event in welding processes.Common Reasons of Porosity
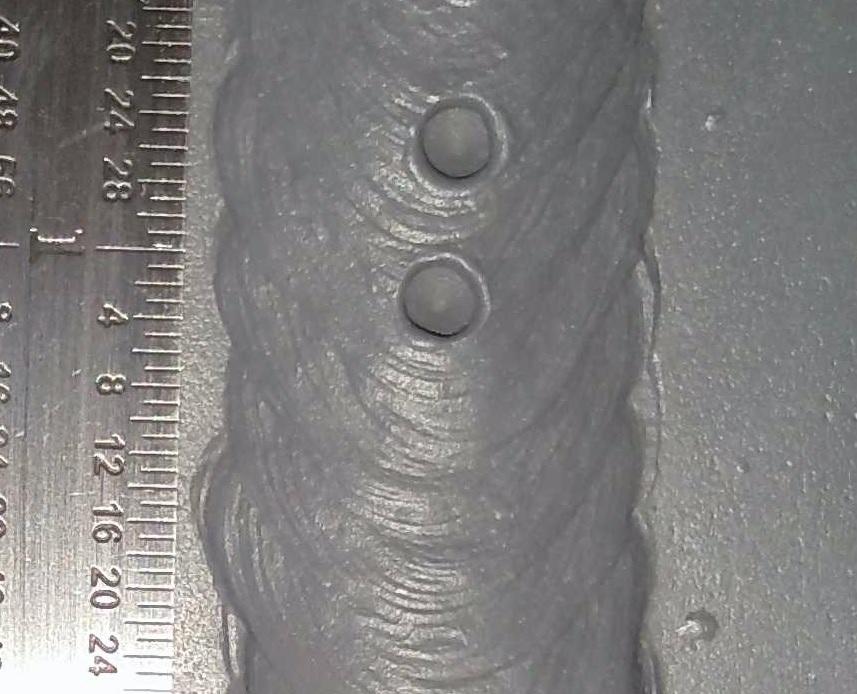
Utilizing dirty or wet filler materials can introduce impurities into the weld, adding to porosity concerns. To minimize these common reasons of porosity, extensive cleaning of base metals, correct securing gas option, and adherence to optimal welding criteria are crucial methods in achieving high-grade, porosity-free welds.
Effect of Porosity on Weld Quality

The presence of porosity in welding can substantially jeopardize the structural stability and mechanical properties of welded joints. Porosity produces spaces within the weld metal, compromising its overall strength and load-bearing ability.
One of the key consequences of porosity is a decline in the weld's ductility and strength. Welds with high porosity levels tend to exhibit lower impact strength and decreased capacity to deform plastically before fracturing. This can be especially concerning in applications where the bonded elements go through dynamic or cyclic loading problems. In addition, porosity can impede the weld's capacity to effectively transmit forces, causing premature weld failing and possible security hazards in important structures.
Finest Practices for Porosity Avoidance
To enhance the structural honesty and high quality of bonded joints, what details steps can be carried out to minimize the event of porosity during the welding process? Using the proper welding strategy for the particular product being bonded, such as changing the welding angle and gun placement, can further stop porosity. Routine assessment of welds and immediate remediation of any type of issues recognized during the welding procedure are necessary techniques to protect against porosity and create premium welds.Value of Proper Welding Methods
Applying appropriate welding methods is extremely important in making sure the architectural integrity and quality of welded joints, building upon the foundation of reliable porosity avoidance steps. Welding methods straight influence the general toughness and longevity of the welded framework. One essential facet view it now of appropriate welding strategies is keeping the right warm input. Excessive warm can lead to enhanced porosity because of the entrapment of gases in the weld pool. Alternatively, inadequate warmth might cause incomplete fusion, producing possible weak points in the joint. Additionally, utilizing the proper welding criteria, such as voltage, existing, and travel speed, is critical for achieving sound welds with marginal porosity.In addition, the choice of welding process, whether it be MIG, TIG, or stick welding, need to line up with the particular requirements of the job to make sure ideal results. Correct cleansing and prep work of the base steel, as well as picking the best filler product, are likewise important components of skillful welding browse around this site strategies. By sticking to these best practices, welders can minimize the danger of porosity formation and create top notch, structurally sound welds.
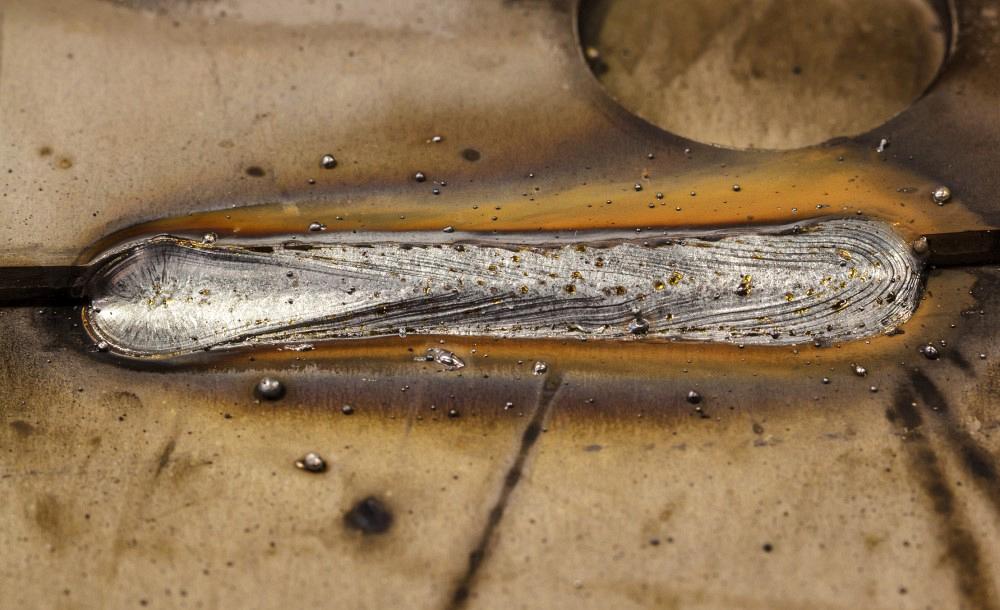
Examining and Top Quality Control Steps
Checking treatments are necessary to detect and stop porosity in welding, making sure the strength and sturdiness of the last product. Non-destructive testing approaches such as ultrasonic screening, radiographic testing, and aesthetic evaluation are generally employed to recognize potential flaws like porosity.Performing pre-weld and post-weld inspections is additionally important in maintaining quality assurance requirements. Pre-weld evaluations involve validating the products, equipment setups, and cleanliness of the workspace to stop contamination. Post-weld assessments, on the various other hand, analyze the last weld for any kind of problems, including porosity, and verify that it satisfies specified requirements. Executing a comprehensive quality assurance plan that includes comprehensive screening treatments and evaluations is paramount to lowering porosity issues and ensuring the total top quality of welded joints.
Final Thought
To conclude, porosity in welding can be a common problem that influences the top quality of welds. By determining the common causes of porosity and carrying out best techniques for avoidance, such as correct welding methods and screening actions, look at these guys welders can make sure top quality and dependable welds. It is vital to prioritize prevention methods to reduce the occurrence of porosity and maintain the integrity of welded frameworks.Report this wiki page